Легированные стали предназначены для изготовления режущего и измерительного инструмента и имеют, по сравнению с углеродистыми инструментальными сталями, большую прокаливаемость, износостойкость и теплостойкость.
Стали для измерительных инструментов
Измерительные инструменты (плитки, калибры, шаблоны) должны сохранять свою форму и размеры в течение продолжительного времени. В них не должны совершаться самопроизвольные структурные превращения, вызывающие изменение размеров инструмента в процессе эксплуатации.
Коэффициент линейного расширения должен быть минимальным. Этими свойствами обладают стали с мартенситной структурой. Для изготовления измерительных инструментов используют стали марок Х, Х9, ХГ, Х12Ф1. Закалка проводится при температурах 850…870 0С в масле. Для устранения остаточного аустенита после закалки проводится обработка холодом при минус 70 0С, а затем низкий отпуск при 120…140 0С. Твердость после термообработки составляет 63…64 НRС.
Стали для режущих инструментов
Основными требованиями к режущему инструменту являются следующие:
- длительное время сохранять высокую твердость и износостойкость режущей кромки в условиях трения;
- иметь высокую теплостойкость (красностойкость), т.е. способность сохранять высокую твердость и режущую способность при продолжительном нагреве (устойчивость против отпуска при нагреве инструмента в процессе работы).
Режущий инструмент изготовляют из сталей, имеющих пониженную или повышенную прокаливаемость, или из быстрорежущих сталей.
К сталям пониженной прокаливаемости относятся углеродистые стали У7…У13, рассмотренные раньше.
К сталям повышенной прокаливаемости относятся легированные стали, содержащие до 5 % легирующих элементов, марок 9ХС, ХВСГ, 9Х5С.
Подобно углеродистым сталям они обладают низкой теплостойкостью – до 300 0С, но более высокой прокаливаемостью. Из них изготовляют инструменты для резания материалов невысокой прочности с небольшой скоростью: ручные сверла, развертки, плашки и др.
Закалку проводят с температуры 800…860 0С в масле, отпуск при 150…200 0С. Твердость составляет 61…66 НRС.
Быстрорежущие стали
К ним относятся высоколегированные стали, предназначенные для изготовления инструментов высокой производительности. Основное свойство этих сталей — высокая теплостойкость (красностойкость), т.е. сохранение мартенситной структуры и высокой твердости, прочности, износостойкости при повышенных температурах, возникающих в режущей кромке при резании с большой скоростью.
Теплостойкость обеспечивается введением большого количества вольфрама совместно с другими элементами: молибденом, хромом, ванадием.
Вольфрам и молибден в присутствии хрома связывают углерод в специальные труднокоагулируемые при отпуске карбиды типа М6С, МС и задерживают распад мартенсита. Выделение дисперсных карбидов, которое происходит при повышенных температурах отпуска (500…600 0С), вызывает дисперсионное твердение мартенсита. При отпуске ванадий, выделяясь в виде карбидов, усиливает дисперсионное твердение.
Увеличению теплостойкости способствует также кобальт. Он не образует карбидов, но, повышая энергию межатомных сил связи, затрудняет коагуляцию карбидов и увеличивает их дисперсность.
За счет комплексного легирования инструменты из быстрорежущей стали сохраняют высокую твердость до 640 0С и допускают в 2…4 раза более производительные режимы резания, чем инструменты из углеродистых и низколегированных сталей.
Быстрорежущие стали обозначаются буквой Р (“рапид” — скорость), после которой ставится цифра, показывающая содержание вольфрама в процентах. Далее указываются легирующие элементы и их содержание в %.
Быстрорежущие стали по эксплуатационным свойствам делятся на две группы:
- нормальной производительности;
- повышенной производительности.
К 1-й группе относятся стали марок Р9, Р18, Р12, Р9Ф5, Р6М3, Р6М5.
Они сохраняют твердость не ниже 58 НRС до температуры 620 0С, лучше обрабатываются давлением, резанием, имеют высокую прочность и вязкость.
Ко 2-й группе относятся стали, содержащие кобальт и повышенное количество ванадия: Р6М5К5, Р9М4К8, Р9К5, Р9К10, Р10К5Ф5, Р18К5Ф2. Они превосходят стали 1 группы по теплостойкости (630…640 0С), твердости (НRС ³ 64) и износостойкости, но уступают по прочности и пластичности. Эту группу сталей применяют для обработки высокопрочных сталей, коррозионно-стойких и жаропрочных сталей с аустенитной структурой, других труднообрабатываемых материалов.
Быстрорежущие стали относятся к карбидному (ледебуридному) классу. В структуре литой стали присутствует сложная эвтектика, напоминающая ледебурит и располагающаяся по границам зерен.
Для придания стали теплостойкости инструмент подвергают закалке и многократному отпуску (рисунок 51).
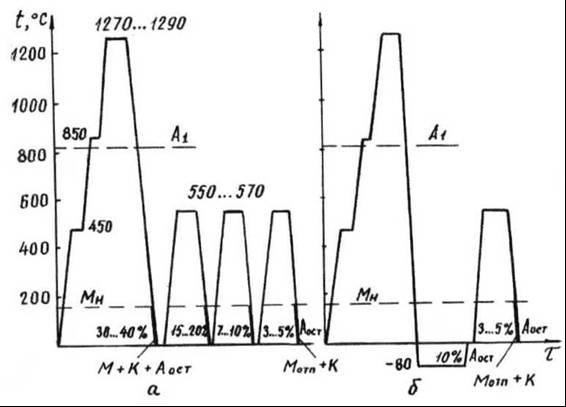
Температура закалки стали Р18 — 1220…1290 0С, Р6М5 — 1210…1230 0С. Высокие температуры необходимы для более полного растворения вторичных карбидов и получения высоколегированного аустенита.
Из-за низкой теплопроводности стали при закалке нагревают медленно с прогревами при 450 и 850 0С. Для уменьшения окисления и обезуглероживания нагрев производится в соляных ваннах (чаще ВаСl2).
Выдержка при температуре закалки должна обеспечить растворение в аустените части карбидов в пределах возможной их растворимости. Для получения более высокой твердости стали Р6М5 (63 НRС) и теплостойкости (59 НRС при 620 0С) выдержку при нагреве под закалку увеличивают на 25 %.
Для уменьшения деформации инструментов применяют ступенчатую закалку в расплавленных солях температурой 400…500 0С. Охлаждение ведется в масле (мелкие детали можно охлаждать на воздухе).
После закалки не достигается максимальная твердость сталей 6HRC, т. к. в структуре, кроме мартенсита и первичных карбидов, содержится 30…40 % остаточного аустенита (Мк ниже 0 0С). Он снижает механические свойства стали, ухудшает шлифуемость и стабильность размеров инструмента. Остаточный аустенит превращается в мартенсит при отпуске или обработке холодом.
Отпуск проводят при температуре 550…570 0С. В процессе выдержки при отпуске из М и Аост выделяются дисперсные карбиды М6С, МС. Аустенит обедняется углеродом и легирующими элементами, становится менее устойчивым и при охлаждении ниже Мн испытывает мартенситное превращение. Применяют двух, трех кратный отпуск с выдержкой по 1 ч и охлаждением на воздухе. При этом Аост снижается до 3…5 %. Обработка холодом сокращает цикл термической обработки. Структура — мартенсит отпуска и карбиды; твердость составляет 65 HRC.