Поверхностная закалка является одним из способов увеличения твердости поверхностных слоев изделия, тогда как его сердцевина остается незакаленной (мягкой вязкой) и хорошо воспринимает ударную нагрузку.
Поверхностную закалку проводят индукционным нагревом током высокой частоты (ТВЧ), газовым пламенем, нагревом лазерным лучом.
Закалка с индукционным нагревом. Индукционный нагрев происходит вследствие теплового действия тока, индуктируемого в изделии, помещенном в переменное магнитное поле.
Для нагрева изделие устанавливают в индуктор (соленоид), представляющий собой один или несколько витков пустотелой водоохлаждаемой медной трубки или шины (рисунок 43).
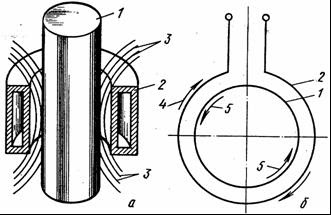
4- направление тока в индикаторе; 5- направление тока в детали
Переменный ток, протекая через индуктор, создает переменное магнитное поле. В результате индукции в поверхностном слое возникают вихревые точки и в слое обрабатываемого изделия происходит выделение джоулевой теплоты. Ток проходит в основном в поверхностном слое металла.
Около 90 % теплоты выделяется в слое толщиной Х (м):

где f- частота тока, Гц;
r — электрические сопротивления материала детали, Ом×м;
m — магнитная проницаемость, Г/м.
Для закалки применяют сравнительно большую мощность (0,1…2,0 кВт/см2), и поэтому время нагрева составляет 2…50 с. Для получения слоя толщиной 1 мм частота тока 50…60 кГц, для слоя толщиной 2 мм — 15 кГц и для слоя толщиной 4 мм — 4 кГц. Обычно считают, что площадь сечения закаленного слоя должна быть не более 20 % всего сечения. После нагрева в индукторе деталь быстро перемещается в специальное охлаждающее устройство — спрейер, через отверстия которого на нагретую поверхность разбрызгивается закалочная жидкость; иногда нагретые детали сбрасываются в закалочные баки.
Высокая скорость нагрева смещает фазовые превращения в область более высоких температур, поэтому температура закалки при нагреве ТВЧ для одной и той же стали должна быть выше, чем при объемной закалке.
Наиболее целесообразно использовать этот метод для нагрева изделий из углеродистых сталей, содержащих более 0,4 % С. Для легированных сталей ТВЧ, как правило, не применяют, так как одно из их преимуществ — глубокая прокаливаемость легированных сталей — при таком методе не используется.
Преимущество метода ТВЧ — высокая производительность, отсутствие обезуглероживания и окисления поверхности детали, возможность регулирования и контроля режима термической обработки, а также полной автоматизации всего процесса.
Недостаток — высокая стоимость индукционных установок и индукторов (для каждой детали свой индуктор), поэтому этот метод экономически целесообразно использовать только при массовом производстве однотипных деталей простой формы.
Закалка с газопламенным нагревом. Этот способ закалки применяют для крупных изделий (прокатных валков, труб, валов и т.д.). Поверхность детали нагревают газовым пламенем, имеющим температуру до 3150 0С. В качестве горючих газов применяют ацетилен ,природный газ, керосин. Для нагрева используют щелевые горелки (имеющие одно отверстие в форме щели) и многопламенные.
Толщина закаленного слоя обычно 2…4 мм, а его твердость для стали с 0,45…0,5 % С — 50…56 HRС. Процесс газопламенной закалки можно автоматизировать и включить в общий поток механической обработки. Для крупных деталей этот способ закалки часто более рентабелен, чем закалка с индукционным нагревом.
Поверхностная закалка при нагреве лазером. Является одним из широко применяемых видов лазерной обработки металлов и сплавов. Она основана на локальном нагреве участка поверхности световым лучом лазера и охлаждения этого участка со сверхкритической скоростью за счет теплоотвода во внутренние слои металла. При этом не требуется применять охлаждающие среды, что существенно упрощает технологию термоупрочнения. Толщина упрочненного слоя не превышает 1,5…2,0 мм.